Hagen/München. Eine Vertauschungsgefahr von unter 0,001 Prozent – von so einer Zahl dürfen viele Logistiker nur träumen. Für Marcus Bleck, der beim Stahlspezialisten Hoesch Hohenlimburg die Brammenlogistik verantwortet, ist diese Quote durch ein neues Lagerverwaltungssystem Realität geworden. Blecks Arbeitgeber, die Hoesch Hohenlimburg GmbH mit Sitz in Hagen (Nordrhein-Westfalen), ist Spezialanbieter für warmgewalzten Bandstahl. Das so genannte „Hohenlimburger Mittelband“ wird in unterschiedlichen Qualitäten aus Brammen hergestellt. Die Anforderungen an die Lagerlogistik des zur ThyssenKrupp Steel AG gehörenden Unternehmens sind hoch: Die angelieferten Stahlbrammen müssen durchgängig fehlerfrei identifiziert werden, um Verwechslungen bei der Aufnahme über die Magnet-Krane auszuschließen. Ein neu implementiertes Lagerverwaltungssystem (LVS) erfasst die durchschnittlich etwa zehn Tonnen schweren, mit Identnummern ausgestatteten Brammen bereits bei der Anlieferung und vergibt die optimalen Lagerplätze. Durch eine präzise Funkortung über „Local Positioning Radar (LPR)“-Stationen, die auf den Kranen angebracht sind, lässt sich die Position der Krane zu jeder Zeit bestimmen. Die Ein- und Auslagerungen kann man so lückenlos zurückverfolgen. Wie die Brammenortung bei Hoesch Hohenlimburg genau funktioniert und welche Verbesserungen der Stahlspezialist durch den Einsatz des neuen LVS erzielt, schreibt das Fach- und Wirtschaftsmagazin LOGISTIK inside in seiner aktuellen Oktober-Ausgabe (10/08). (pi) Heft online bestellen – hier klicken: http://www.logistik-inside.de/cms/689692 Telefonische Bestellung unter: 0180 / 500 92 91 (bundesweit nur 0,14 Euro pro Minute aus dem dt. Festnetz/Mobilfunk abweichend).
Thema der Woche: Brammenlager in 3-D
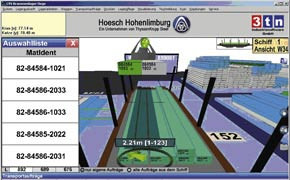
Der Stahlspezialist Hoesch Hohenlimburg steuert seine Brammenlogistik mit einer ausgefeilten IT-Lösung. Funkortung an Kranen sorgt für Prozesssicherheit